If you want to make symmetrically round copper parts, then spin forming is your best metal fabrication technique.
The best part – this article provides in-depth information on the copper spinning process regarding types, benefits, applications, tools, etc.
Sounds interesting? Let’s dive in!
Copper Spinning
As the name suggests, copper spinning refers to spinning a copper tube or disc at a higher speed. Doing this allows you to create axially symmetric components.
Types of Copper Spinning
There are multiple types of spinning processes exist. You can choose anyone focusing on your requirements depending on end applications. Some critical types for your consideration are:
Conventional Spinning
Conventional spinning also refers to cold metal spinning. In this process, you need to utilize the circular preformed copper sheet.
The process begins by placing this sheet right between the mandrel and clamp. This then follows a high-speed rotation. Later it would help if you used a rigid tool to facilitate the shaping or deformation of a particular material. It would help if you forced the device against the spinning metal piece to achieve the desired shape.
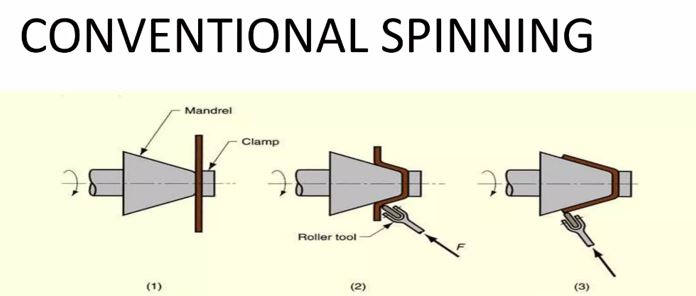
You can utilize both power and manual spinning in the conventional spinning process. This contributes to getting the axially symmetric end product.
Tube Spinning
You must use a hollow metal blank (cylindrical form) instead of a metal sheet in this copper spinning process. You must place the hollow tube on the mandrel and clamp it with the tailstock to prevent slipping.
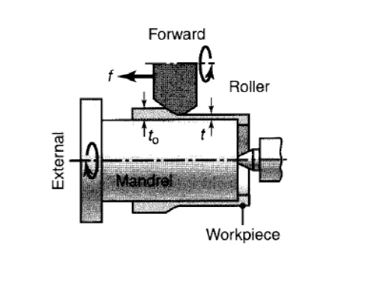
You can use the rigid tool internally as well as externally. Doing so will result in reducing the thickness and formation of a long tube. When conducting the internal finish, the hollow mandrel serves the part best in this regard.
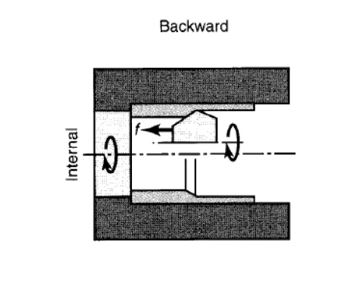
Shear Spinning
Shear spinning is similar to that conventional spinning. The shear spinning is spinning in which the end product dia is identical to the dia of a metal sheet.
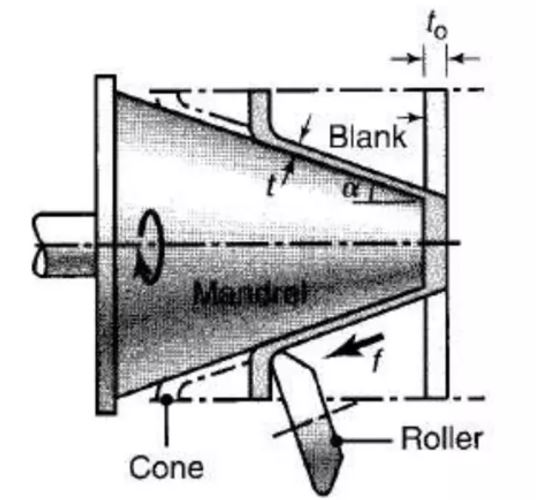
You must put the metal blank right between the tailstock and mandrel to initiate the copper spinning. The shape of the mandrel in shear spinning is similar to that of the interior of the end product you desire.
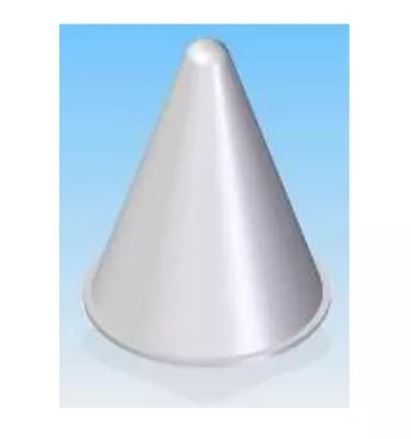
On high-speed rotation, the metal blank takes up the shape of the mandrel. You can see the image for a better understanding. In this process, you can experience the reduction of metal thickness.
The machine you use in the shear spinning process is similar to conventional spinning. The only difference is it is more robust and caters to higher force requirements. This will lead you to perform the shearing operation more effectively.
Hot Spinning
Hot in hot spinning refers to heating the metal blank before subjection to the spinning process. This is true, especially when dealing with thicker metals that do not facilitate processing at room temperatures.
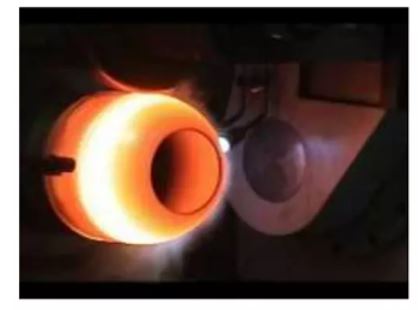
In this process, you put the blank over the mandrel and offer support or clamping with the tail post. Following the high-speed rotation, the metal blank takes up the form of the mandrel.
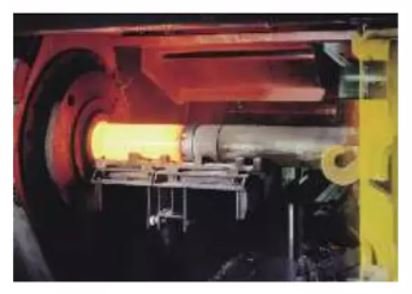
Copper Spinning Tools
Several tools assist in the copper spinning process. Without these tools, you cannot obtain the specific form of finishing you need. Get insights into some essential tools in the spinning process right below.
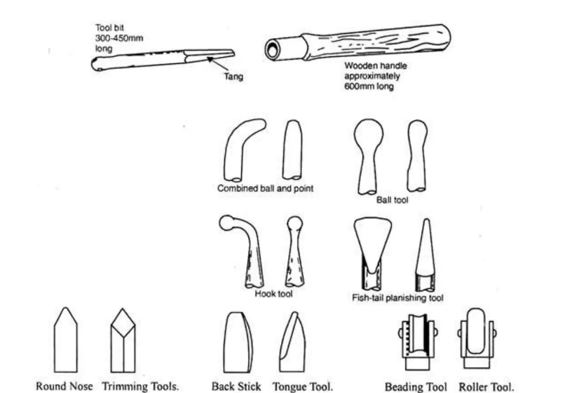
Internal
To process internal tooling, you need to place the metal blank over the mandrel
- Combined ball and point
- Tang
- Hook tool
External
To initiate external tooling requires you to place the metal piece right inside the hollow mandrel
- Roller tool
- Beading tool
- Round Nose
- Trimming Tool
Collapsible
The collapsible tooling refers to the tooling you utilize on varying diameter parts to process material shaping/removal.
- Tongue tool
- Fish Tail
- Back stick
Copper Spinning Shapes
A multiple shape you can experience when subjecting your copper to spinning. The basic shapes are the following for your reference:
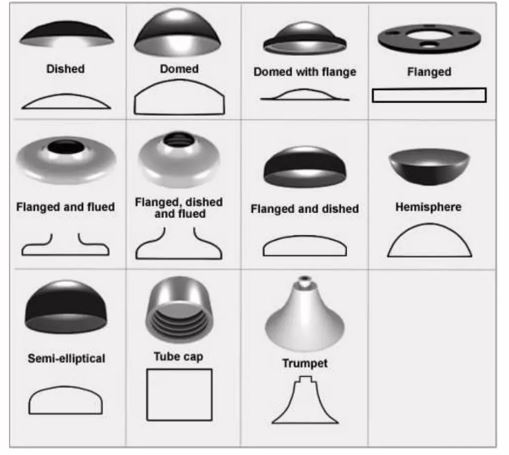
Dished
This shape is defined as curving inward or patelliform concave, resembling the pan or dish.
Flanged
You can refer to a flange as a collar or rim projecting out from the object similar to that of a beam or column
Flanged and flued
The shape refers to the annular plates having outside edges in one direction and inside edges in another direction
Hemisphere
A circular shape having a flat face as well as a curved surface area
Semi-elliptical
It is a shape having a form similar to one-half of the ellipse
Domed with Flange
It refers to the combination of the dome as well as the flange to facilitate snap lock
Trumpet
Trumpet refers to a round, oblong shape having a similar appearance to a wedge-like shape
Domed
A dome refers to the form that resembles half of a sphere
Benefits of Copper Spinning
A series of benefits exist when you deal with copper spinning. Find the key ones that need your attention right below:
Low Waste
Copper spinning will not be going to result in metal waste. This means you can save up more metal. Also, spinning prevents your time to clean the vicinity from scrap waste.
Cost Effective
When it comes to cost, you can save a lot with copper spinning compared to other metalworking methods. This method ensures quality manufacturing by keeping the cost low.
Time Saving
You don’t need to pass the metal to various finishing processes after or before metal working. This will help you save time drastically. Just following a single process operation, you can manufacture what you want.
Dynamic
Copper spinning methods allow you to make use of any size as well as the type you want. There is no limit on the types of end shapes you can obtain while working with this method. Copper spinning is dynamic in the true sense.
High Durability
The copper spinning process improves the end properties or characteristics of materials. It makes the end product more tough, strong, as well resilient. The main reason behind this is the repetitive forces’ impact.
Applications of Copper Spinning
A wide range of applications exists for copper spinning. In this section, you will find insights into notable uses of copper spinning.
Agriculture
You cannot overemphasize the importance of copper-spinning products in agriculture. The key components include funnel feeders, discs, plate covers, rollers, and jumpers. You can also use them in various agricultural machines for crucial component manufacturing.
Automotive
You can manufacture the vehicle headlight or backlight housings using copper spinning. With this technique, you can also manufacture motor housings. In the vehicle’s electrical accessories, you can also use the copper spinning product. This is because they ensure higher electrical conductivity.
Marine
The applications of copper spinning products in the marine industry are endless. You can manufacture any component like pump housing, seawater piping, aquaculture cages, condensers, marine fittings, pump housing, etc.
Foodservice Lighting
Copper-spun products have higher desirability among various restaurants. Especially in the form of light housings. The ambiance they create and accentuate the vicinity is remarkable.
Commercial Roofing
The benefits of copper as a roofing material are endless. This is where you can use copper spinning methods to curate different styles and shape roofing products. The desirability of copper roofing products is because they last for life.
Satellite Dish
You can use metal spinning methods to create the satellite dish. As the satellite dish needs to be in the atmosphere for longer. Copper ensures optimum performance by strongly resisting rust, corrosion, and weather impact.
Conclusion
Many products around us indeed follow copper spinning techniques to ensure their existence. After reading the above article, you can create any copper product by the copper spinning methods you want. Try any one of the techniques mentioned above.
More Resources:
Shear Forming – Source: Wikipedia
Metal Spinning – Source: Wikipedia
Spinning Metal – Source: IQS Dircetory